Preventative Maintenance, Technology, and Visit Frequency
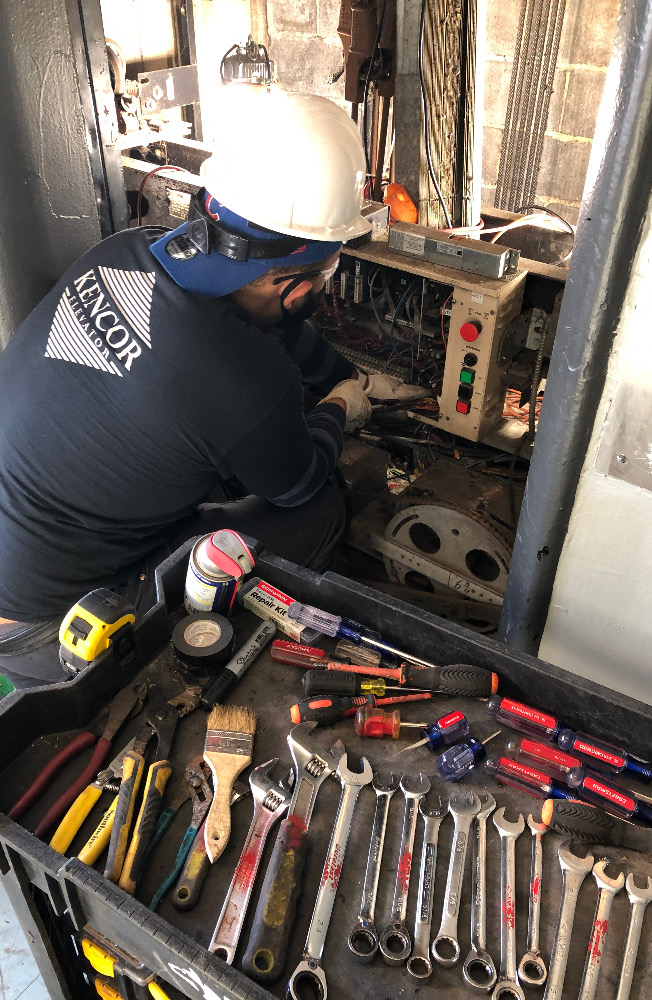
(Technology should only be utilized to compliment the overall quality of the maintenance; not replace it)
As technology continues to increase and advance there is an unsettling trend and misconception within the elevator industry. Are skilled technicians and elevator maintenance less relevant than in years past? In actuality, they are more vital than ever.
Equipment
As technology continues to advance, the mechanical nature of equipment requires less maintenance. In the past, controllers were made from relays which have been replaced by solid-state boards. In addition, today’s elevators can be equipped with monitoring devices and sensors which allow for remote monitoring capabilities. On the surface, these advancements allow for less maintenance when compared to their predecessor systems.
Labor
Throughout the history of the industry the norm was to provide for 1 hour of maintenance, per month, per elevator for hydraulic elevators and at least 2 hours for traction elevators. Due to the time spent at the facility the technician was able to become familiar with the equipment and become more adept at identifying failures before they happened.
Currently, the trend in the industry for the larger OEM’s is to cut costs by visiting properties less and by spending less time at the property when they do arrive. This has driven the industry to quarterly maintenance visits, as opposed to monthly, or even worse to provide maintenance when they arrive for a service interruption.
Effects
By attempting to control labor costs, driven by the need to produce suitable financial results, we have found ourselves in the era of the “super” or “mega” route. Typically, these routes consist of 200-400 units per route. Tasks include maintenance, service calls, repairs, and testing for the entire portfolio that encompasses the route.
The OEM’s response to the disconnect between available labor hours and maintenance labor hours required is to utilize remote monitoring devices. Remote monitoring devices are intended to detect problems on the elevator without the need for human intervention. There is no question that remote monitoring devices can be a useful tool for elevator companies. However, issues arise when remote monitoring is implemented to eliminate all human intervention.
Additionally, remote monitoring devices fail to achieve requirements of the ASME A17.1 safety code such as fireman’s service and emergency communication devices. Without regular maintenance visits the elevator is unable to benefit from corrections to operating and signaling devices, rail lubrication, floor stops, and overall lubrication of mechanical components.
Conclusion
Technology can certainly make the industry safer and more efficient but using technology as a substitute for regular maintenance and human intervention degrades the lifespan of the equipment and puts the public invitee at risk. Regular visits from skilled technicians can spot trouble before they turn into costly repairs and service interruptions. Technology should only be utilized to compliment the overall quality of the maintenance not replace it.